Printed circuit board (PCB) fabrication is a critical component of modern electronics manufacturing. As the foundation upon which all electronic components are mounted, PCBs must meet stringent quality standards to ensure reliable and precise performance. Poor-quality PCBs can result in malfunctioning products, costly recalls, and reduced device lifespans.
In this blog, we will explore why PCB fabrication quality matters and offer tips for ensuring precision in your PCB manufacturing process.
The Importance of PCB Fabrication Quality
The quality of a PCB affects the overall performance, longevity, and safety of electronic devices. Whether you’re designing consumer electronics, medical devices, or industrial systems, the PCB plays a crucial role in the functionality of your product. Here’s why quality matters:
Signal Integrity
PCBs are responsible for routing electrical signals between components. High-quality fabrication ensures that these signals are transmitted without interference or degradation. Poor-quality PCBs may have design flaws such as inconsistent trace widths or incorrect layer alignment, which can result in signal loss, delays, or cross-talk between circuits.
Mechanical Durability
PCBs need to withstand various environmental stresses, including vibration, heat, and mechanical pressure. Precision fabrication ensures that the board can endure these stresses without cracking, warping, or breaking. Low-quality materials or fabrication techniques can lead to premature failure of the board, reducing the lifespan of the overall product.
Component Placement Accuracy
Precise PCB fabrication ensures that components are placed accurately on the board. Even slight misalignments can result in poor electrical contact or soldering issues, leading to malfunctions during operation. High-precision fabrication ensures that components fit perfectly, improving overall reliability.
Thermal Management
PCBs are often used in devices that generate significant heat. High-quality fabrication ensures proper thermal management, helping to dissipate heat from components. This is critical for preventing overheating, which can damage components and reduce the device’s lifespan.
Common Issues in Poor-Quality PCB Fabrication
Several issues can arise from poor-quality PCB fabrication, affecting both the performance and reliability of the end product. Below are some of the most common problems:
Delamination
Delamination occurs when the layers of the PCB start to separate due to poor bonding during the lamination process.
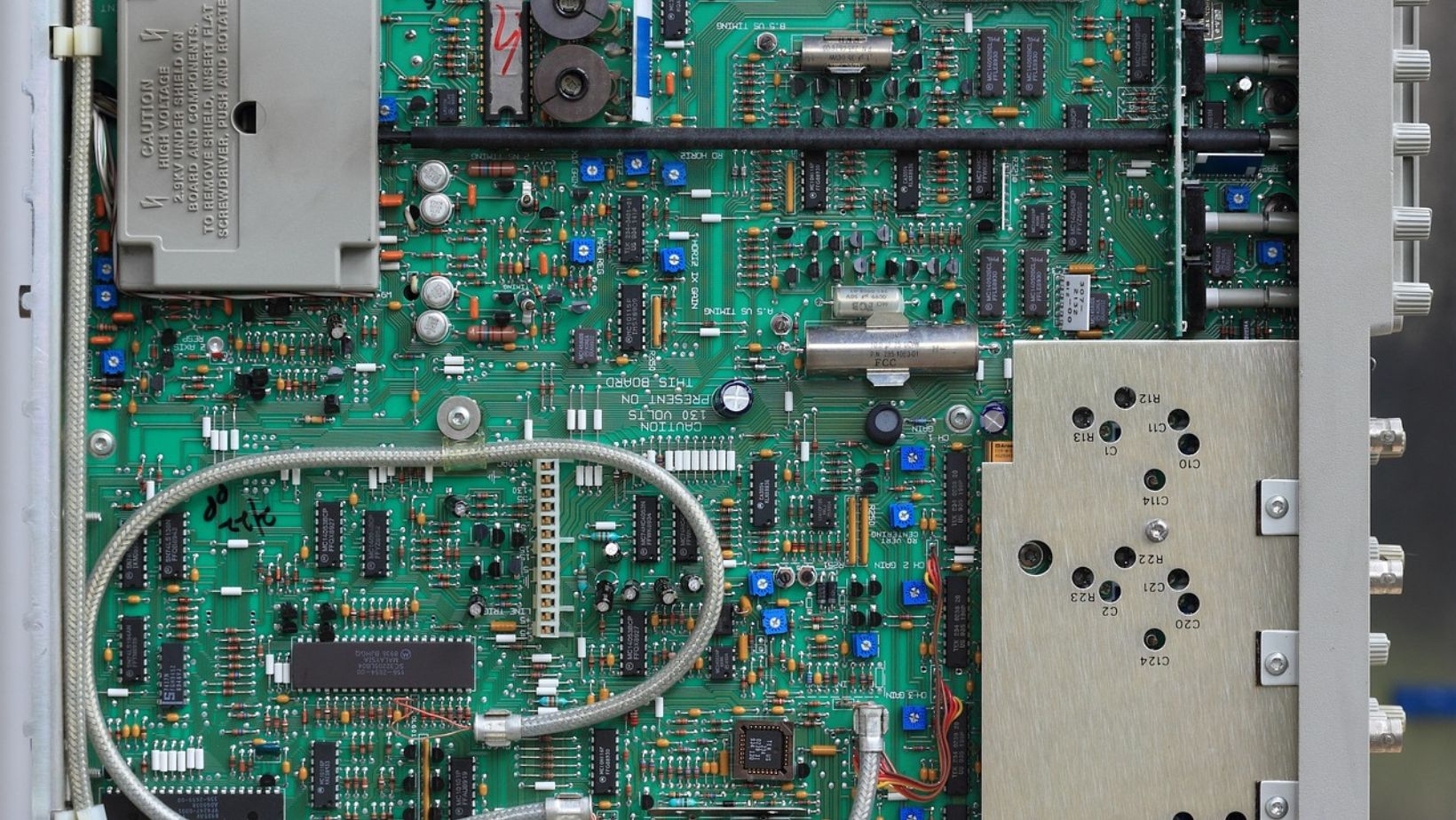
This can cause electrical failure, as the separated layers interfere with the board’s ability to conduct signals properly.
Solder Mask Issues
The solder mask is a protective layer applied to the surface of the PCB. Poor-quality fabrication can result in uneven or improperly applied solder masks, leading to exposed traces, short circuits, or contamination during soldering.
Misaligned Drill Holes
Drill holes, or vias, are used to connect different layers of a PCB. Misaligned or inaccurately drilled holes can cause electrical connectivity issues, leading to failure of the entire circuit. Precision drilling is essential for ensuring proper layer-to-layer connections.
Warping and Bending
PCBs that are not fabricated with proper materials or techniques can warp or bend under stress. This can lead to poor component alignment and electrical issues. Warping is especially problematic for multi-layer boards, where the misalignment of layers can disrupt signal transmission.
Tips for Ensuring Precision in PCB Fabrication
Ensuring precision in PCB fabrication requires attention to detail and adherence to best practices. Below are some tips for achieving high-quality PCBs:
Choose the Right PCB Manufacturer
One of the most important steps in ensuring PCB fabrication quality is choosing a reputable manufacturer. Look for manufacturers with a proven track record of delivering high-precision PCBs. Factors to consider when choosing a PCB manufacturer include:
- Certifications: Ensure that the manufacturer is certified for industry standards such as ISO 9001 or IPC-A-600, which reflect their commitment to quality.
- Advanced Equipment: A manufacturer that uses the latest fabrication technologies, such as automated optical inspection (AOI) and laser drilling, will be better equipped to produce precise and reliable PCBs.
- Customization Options: Look for manufacturers that offer customization to meet the specific needs of your application, whether it’s material selection, layer count, or trace width tolerances.
Opt for High-Quality Materials
The choice of materials plays a key role in the precision and reliability of your PCB. Common materials include FR-4 (a fiberglass-reinforced epoxy), polyimide, and ceramic. Each material has different thermal and electrical properties, so it’s crucial to select one that matches the needs of your project.
- FR-4: Ideal for general-purpose applications.
- Polyimide: Suitable for high-temperature environments or flexible circuit designs.
- Ceramic: Best for applications requiring excellent heat dissipation and thermal management.
Investing in high-quality materials will result in better mechanical durability, signal integrity, and thermal performance.
Optimize PCB Design for Manufacturability
The design of your PCB has a significant impact on the quality of the final product. Optimizing your design for manufacturability (DFM) ensures that your board can be fabricated with precision and without errors. Here are some key design tips:
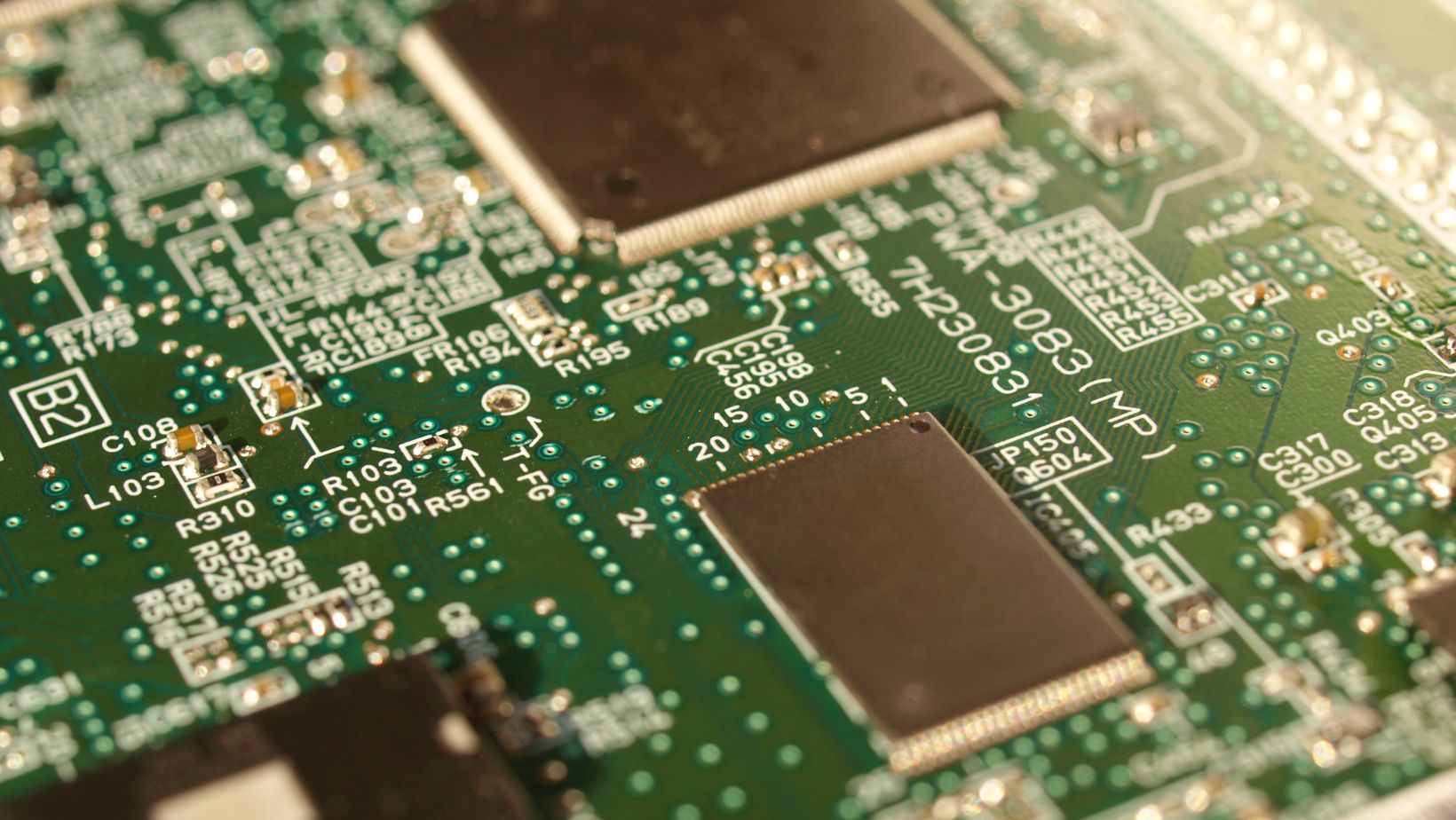
- Maintain Adequate Trace Spacing: Ensure there is enough space between traces to prevent short circuits or interference.
- Standardize Hole Sizes: Consistent hole sizes make the drilling process more accurate and reduce the risk of misaligned vias.
- Consider Thermal Relief: Proper thermal management design, such as thermal relief pads, ensures efficient heat dissipation during the soldering process.
Collaboration with your manufacturer during the design phase can help identify potential issues early on, reducing the likelihood of fabrication errors.
Implement Rigorous Testing
Testing is a crucial part of ensuring PCB quality. Both the manufacturer and designer should implement rigorous testing protocols to verify that the board meets all specifications. Common testing methods include:
- Automated Optical Inspection (AOI): Used to inspect for surface defects such as open circuits, shorts, and misaligned components.
- X-ray Inspection: Allows for the examination of internal layers and vias to detect hidden defects.
- In-Circuit Testing (ICT): Ensures that the electrical performance of the board is correct by testing each component’s functionality.
- Functional Testing: Simulates real-world operating conditions to ensure the PCB performs as intended in its final application.
By conducting thorough testing at multiple stages of the fabrication process, you can catch and fix any issues before the board goes into full production.
The Role of Technology in Precision PCB Fabrication
Advances in technology have significantly enhanced the precision and reliability of PCB fabrication. Tools like Laser Direct Imaging (LDI) enable the creation of finer traces and more accurate layer alignment, ensuring higher-quality boards. Automated Optical Inspection (AOI) allows manufacturers to quickly detect surface defects such as misaligned components or open circuits, reducing the risk of errors.
Additionally, High-Density Interconnect (HDI) technology enables more compact designs by incorporating finer traces and smaller vias, which is essential for space-constrained applications like smartphones and wearables. These innovations collectively help manufacturers achieve greater precision, resulting in better performance and reliability for electronic devices.
Conclusion
The quality of PCB fabrication is fundamental to the performance and longevity of any electronic device. Precision in fabrication ensures signal integrity, mechanical durability, and proper component placement, all of which contribute to the reliability of the final product. By selecting a reputable manufacturer, choosing high-quality materials, optimizing your design, and implementing rigorous testing protocols, you can ensure that your PCB meets the highest standards of quality and precision. With advancements in fabrication technology, achieving precision has never been more accessible, helping to push the boundaries of modern electronics.